The automotive industry is in a state of constant evolution, driven by the adoption of advanced technologies that enhance quality, efficiency, and safety in production lines. One of the most impactful innovations is machine vision, a technology that uses cameras to extract valuable information from digital images, optimising decision-making and automating complex tasks.
Machine vision cameras play a key role in this transformation. They provide real-time data essential for the automated systems in the automotive industry. This article focuses on evaluating and comparing different camera technologies, with a particular focus on hyperspectral cameras, which are revolutionising inspection and supervision applications thanks to their ability to reveal details not visible with conventional technologies.
Technological diversity in machine vision cameras
RGB cameras: These cameras, which capture images in red, green, and blue, are fundamental in applications where colour perception is critical. They are ideal for inspecting painted surfaces and monitoring the quality of manufacturing processes, although their performance can decrease in low light conditions and they are not the best for measuring distances.
Monochrome cameras: Operating in grayscale, these cameras eliminate the need for colour processing, allowing them to offer higher contrast and sensitivity in dark environments. They are effective for verifying the presence and alignment of components and detecting surface defects.
Infrared or thermal cameras: Used to detect thermal radiation, these cameras are crucial for identifying issues such as overheating or material defects through thermal analysis, though their image resolution is generally lower than other machine vision cameras.
3D vision cameras: Using techniques such as stereoscopy or time of flight, these cameras provide a three-dimensional image of the inspected object, facilitating complex tasks such as dimensional inspection and robotic manipulation of components.
The transformative role of hyperspectral cameras
Hyperspectral cameras represent a qualitative leap in machine vision technology. These devices not only identify surface defects as conventional cameras do, but they are also particularly useful for inspecting coatings and paints, detecting contaminants and unwanted particles in components, and analysing the composition of materials.
This is crucial to ensure the durability and quality of products, making them invaluable in the automotive industry, all with high precision.
With the implementation of advanced machine learning technologies and continuous improvements in data processing, hyperspectral cameras have the potential to radically transform manufacturing processes in the automotive industry. They elevate quality and efficiency standards to unprecedented levels, solidifying the automotive industry at the forefront of technological innovation.
However, several challenges are faced in the implementation of hyperspectral technology. The capture speed of these cameras is relatively low compared to conventional cameras, which can compromise the efficiency of production processes that require rapid inspections. Additionally, processing hyperspectral data requires advanced programming and entails a high computational load. These challenges could be mitigated with the development of more efficient algorithms and the application of emerging technologies such as machine learning and cloud computing.
Another significant obstacle is the complexity of integrating these cameras into industrial environments, which demands specific hardware and precise calibrations. Adaptability and automation in calibration systems are essential to simplify the implementation of hyperspectral cameras in production lines, improving efficiency and fully leveraging the capabilities of this technology in the automotive industry.
Success story: A 300% improvement in computation time
Innovative projects such as those led by CT are advancing the use of hyperspectral vision. These initiatives aim not only to increase data capture speed but also to improve the precision and quality of analysis, ensuring that vehicles meet the highest quality standards.
The project focused on optimizing hyperspectral camera data processing to enhance image capture with potential applications in the automotive industry. The main objective was to optimise hyperspectral image capture, generate spectral data for decision models, and validate data and machine learning algorithms in a laboratory prototype.
For ease of access to test products, it was decided to train advanced hyperspectral vision tools by evaluating the quality of fruits and vegetables. The work included identifying aspects such as sugar content and detecting bruises by creating specific hyperspectral libraries.
The results have been significant: capacities for defining chemometric bases of test elements and their subsequent analysis have been generated, machine learning algorithms for detecting bruises and surface defects have been developed, and a graphical interface for visualizing and interacting with the results
has been constructed. Additionally, a 300% improvement in computation time was achieved using a Principal Component Analysis (PCA) model that reduced the information from images of 224 spectral bands to a three-dimensional vector without losing precision.
Future prospects
As previously mentioned, machine vision cameras are setting a new standard in vehicle manufacturing. Hyperspectral cameras, in particular, offer a detailed and in-depth view of materials and processes, going beyond the limitations of conventional technologies. The successful integration of these cameras into production lines not only improves quality and safety standards but also promotes operational efficiency.
Therefore, true to CT’s mission of applying the latest digital tools to enhance the efficiency and effectiveness of our clients, the next objective in this research area will be the application of the results obtained in a mass production industrial environment, specifically focusing on detecting surface defects in the automotive sector.
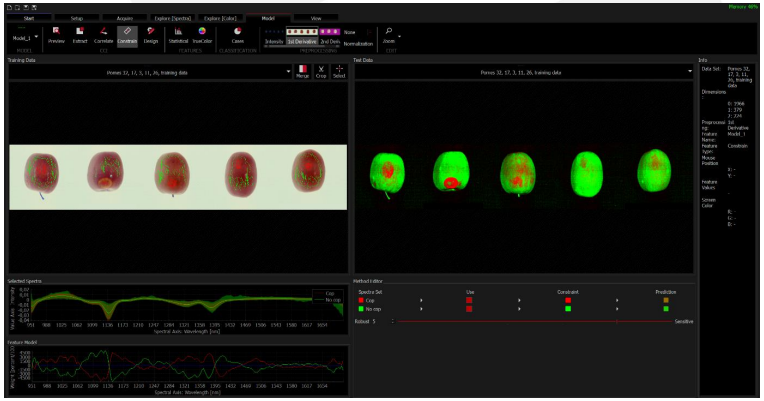
Classification model for hyperspectral images of bruised apples On the left side of the screen are the training images, and on the right, the images to be analysed.