CT, a leading technology company providing innovation and engineering services throughout the product lifecycle, presents the progress of the first year of work on the ADDHOC R&D initiative, a solution for the custom manufacturing of metal parts for applications with high mechanical performance, short manufacturing runs and customized geometries using additive manufacturing technologies. ADDHOC’s challenge is to create flexible solutions that improve the connectivity between complex manufacturing processes and their associated means, to investigate the automation of additive manufacturing and to increase knowledge in advanced metallic materials thanks to the application of digitalization and, in particular, of Artificial Intelligence, simulation and vision technologies.
Through ADDHOC, CT and its partners in the consortium, seek to facilitate the entry of these mature technologies into manufacturing companies, combining the knowledge gained in previous projects for the development of machines, additive DED processes and materials, with digital development of new software tools. The initiative responds to several technological and market aspects, such as a growing demand for precision and quality of machined parts, increasingly demanding lead and production times, and the much desired reduction of manufacturing costs in medium-high added value processes.
After a year of research, the participating companies are closer to completing the virtual prototyping process, which makes it possible to simulate and model the manufacturing of components at the software level, by means of the:
- Development of simple programming tools, CAD, of parts focused on DED technologies (WAAM and LMD).
- Development and fine-tuning of calculation and simulation tools, CAE.
- Development of part programming tools, CAM.
Finally, to validate all the tools developed, the demonstrators proposed by the end users – ABC Compressors and EIPC – will be manufactured:
- Validating the cyber-physical system, synchronizing the data obtained in the virtual prototyping stage and the data acquired during component manufacturing.
- Communicating with the machine during demonstrator manufacturing.
- Developing empirical mathematical models capable of correlating real parameters with virtual prototyping.
CT’s team of experts, already experienced in additive manufacturing after the Haritive project, is in charge of the dynamic CAD/CAM/CAE development through the integration of process data in the initial theoretical calculations, as well as the development of software environments based on Big Data and Machine Learning strategies.
The consortium led by CT is formed by multidisciplinary companies with extensive experience in high deposition additive manufacturing projects acquired in previous Hazitek calls (HARITIVE, HARIPLUS, WAAMTOOL), including: ADDILAN, Sonosti Soldadura, AIPC, ABD Compressors, Tecnalia Research and Innovation and the University of the Basque Country, as a collaborating entity.
ADDHOC is part of “Smart Industry”, one of the three strategic priorities included in the new “2030 Basque Science, Technology and Innovation Plan ” (PCTI Euskadi 2030). By combining metal additive manufacturing technologies with digital tools, CAx, this project will provide a technical leap forward for Basque industry.
About ADDHOC
Project Customized manufacturing of metal parts for applications with high mechanical performance, short manufacturing series and customized geometries by means of additive manufacturing technologies (nº ZL-2021/00989). The project is framed within the Support Program for Business R&D – Hazitek, an action co-financed by the Basque Government and the European Union through the European Regional Development Fund 2021-2027 (Feder).
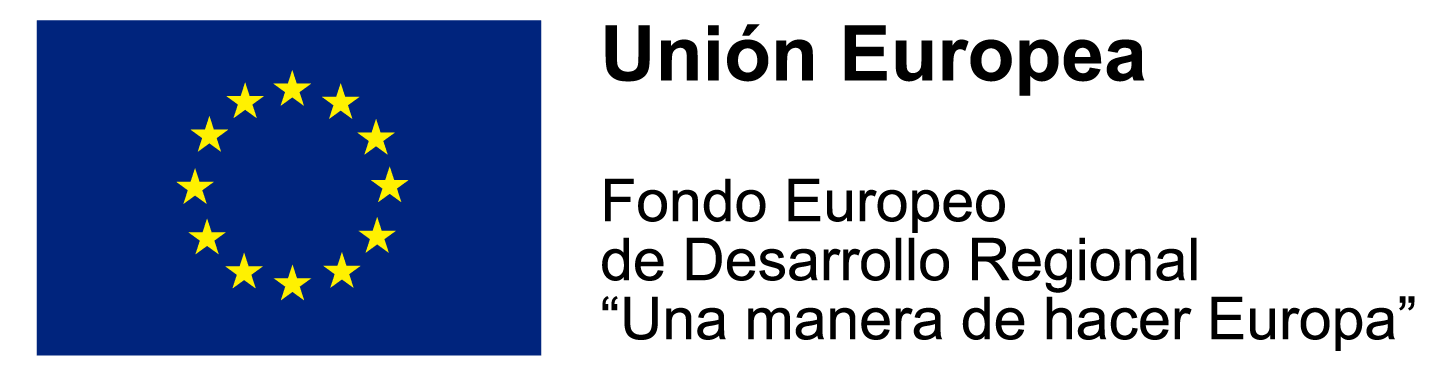
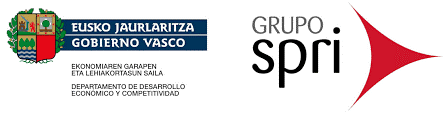